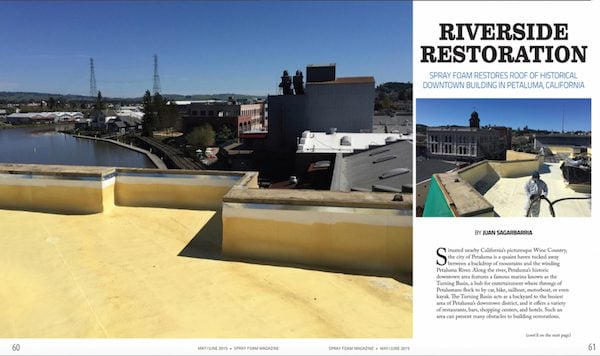
Riverside Restoration: Spray Foam Restores Roof of Historic Downtown Building in Petaluma, California
BY JUAN SAGARBARRIA Spray Foam Magazine โ May/June 2015
Situated nearby Californiaโs picturesque Wine Country, the city of Petaluma is a quaint haven tucked away between a backdrop of mountains and the surrounding Petaluma River. Along the river, Petalumaโs historic downtown area features a famous marina known as the Turning Basin, a hub for entertainment where throngs of Petalumans flock to by car, bike, sailboat, motorboat, or even kayak. The Turning Basin acts as a backyard to the busiest area of Petalumaโs downtown district, and it offers a variety of restaurants, bars, shopping centers, and hotels. Such an area can present many obstacles to building restorations.
In the case of a recent spray foam roof restoration for a three-story retail building located next to the Turning Basin, many challenges such as weather delays, foot traffic, and overspray issues had to be taken head-on. Notwithstanding, Wedge Roofing turned to their comprehensive spray foam roofing expertise to swiftly complete the application.
โIt was a tough application because there were many different factors that could easily have caused the project to go south,โ said Wedge Roofingโs Gary Harvey. โPrevailing winds were a considerable threat due to the height of the building and the proximity to the Petaluma River. We did not allow the spray foam operations to impact the marina or its vessels, not to mention the nearby historic buildings. We were working regular hours so there was always a great number of people walking around the building.โ
To complicate matters further, there was a popular wine bar and restaurant on the buildingโs first floor that refused to lose business by closing their doors during the roof restoration. Because of this, Wedge had to apply the spray foam without tearing off the existing roof off for fear of disposed debris affecting the restaurant patrons, particularly in the patio area. Parking was also an issue for the Wedge crew. With a special access permit, they could only park their rig in a designated spot on a walkway adjacent to the building. The parking spot was located 15 feet away from the restaurantโs entrance, so pedestrians and onlookers were a constant presence. To provide safety for these individuals, Wedge was responsible for redirecting foot traffic throughout the projectโs duration.
โObviously, this job called for extra labor, both on the roof and on the ground. We had to have one person on the ground at all times redirecting pedestrians and folks who were going into the restaurant,โ said. โHe acted as our liaison between parking officials, the restaurant, and our crew.โ
Along with the crewmember in charge of perimeter delineation, Wedge had a six-man team onsite consisting of sprayers, spray shield holders, and a rig operator. The crew was outfitted with PPE that included Tyvek suits, gloves, and 3M 5201 half-face organic respirators. Once their rig was securely parked, the crew pulled the 300 feet of hose connected to their Graco E-30 proportioner and Graco GH 933 Big Rig hydraulic sprayer up to the roof and worked from there. Their job consisted of applying spray foam to the cap sheets of the existing built-up roof, mainly to address numerous leaks that had contributed to the buildingโs gradual deterioration.
โAlthough it was a modern building compared to some of the historic buildings nearby, it definitely needed a new roof,โ said Harvey. โWith spray foam, the roof could be tightly air-sealed, and the building would also benefit from the insulating value.โ
Aside from the 3,500 sq. ft. flat roof surface, the project also included spraying the perimeter parapet walls. Since the parapet walls had existing metal cap flashing that could not be detached, the Wedge crew installed five-inch custom counter-flashing to the parapet walls in order to terminate the foam to the metal.
โThe existing perimeter metal was an integral part of the exterior faรงade of the roof,โ said Harvey. โRemoving the metal would have resulted in the building necessitating a considerable amount of exterior cosmetic repair, so the counter-flashing installation was essential in this case.โ
Using a Graco Fusion AP gun, the Wedge crew installed to the flat roof and parapet walls one inch of PREMISEAL 280, a 2.8 lb. spray foam formulated by Premium Spray Products (PSP). During the SPF application, Wedge crewmembers handled multiple spray shields consisting of sheet cloth attached to wooden-frames around the sprayer to reduce wind and mitigate overspray. Harvey noted that as many as three crewmembers at a time held windscreens around the sprayer depending on the area of the roof that was being sprayed.
For the coating application, the Wedge crew used PSPโs PREMICOTE 2100, a white, high-solid, San Francisco Bay Area-compliant silicone coating. They used a Graco XTR-7 airless spray gun to install a gallon and a half of PREMICOTE 2100 in a single pass. Once the silicone coat had cured, the crew embedded Lucas Specialty Rockโs #11 fire white granules into a second half-gallon pass of coating. The granules were broadcasted by hand at 30 pounds per 100 sq. ft. due to the lack of parking for the machinery that sprays granules and the relatively small roof area.
Additionally, the Wedge crew replaced a broken access hatch on the roof with a new, BILCO paint finish hatch. The process entailed removing the existing hatch, fastening the new metal hatch to the roof using lag-type wood fasteners, priming the new hatch with PSPโ PREMICOTE P75, and finally integrating the newly secured hatch into the roof system.
It took nearly four days for the Wedge crew to wrap up the spray foam roof installation and roof access hatch replacement prior to the projectโs final inspection with the building owner. According to Harvey, the owner was pleased with Wedgeโs work, particularly the long-term benefits it provided and the minimal impact to the building occupants.
โThe building now has a fully sustainable roof system, which provides the building with a whole new life,โ said Harvey. โIf recoated at the recommended intervals, this will be the last system this building ever needs. This spray foam roof is going to provide the building owner and occupants with insulating and reflective qualities that no other system can offer.โ